Techniques and Patent
Powder Metallurgy
- Powder metallurgy products can be used in industries such as automobiles, home appliances, hand tools, sewing machines, electronics, sports equipment etc.
- The powder material is iron-based, copper-based, copper-iron-based, and stainless steel-based.
- PM with porous characteristics, oil-containing bearings has a self-lubricating effect and can be used for a long time without oil injection.
- For those products with complex shapes and difficult machining, the cost can be reduced through the powder metal process.
- High production efficiency, suitable for mass production to reduce costs.
- The density of powder metal product can reach 5.8~7.2 g/cm3.
Powder forging
- Powder forging is a technique that combines the advantages of PM and forging.
- It has some great features, such as enhancing the density and strength of the products, decrease the loss of material and suitable for mass production.
- Currently powder forging products are widely used in automobile, mechanics, aeroplane and other industries.
- The density of powder forging product can reach 7.7~7.8 g/cm3.
Powder forging (PF)
metallographic Comparison
density 7.8 g/cm3
Before PF(Obvious pores)
After PF(compact structure)
Forging
- Forging products are suitable for applications which require high strength and high impact force.
- Hot forging is done in the temperature higher than recrystallization temp of material.
- It can enhance the malleability and inner quality of the products.
High density PM (Powder Metallurgy)
- In order to meet the demand of lighter, smaller, stronger parts for applications in automobile, 3C and mechanics industries, we develop a high density PM solution.
- We are able to offer our service from material choice to tooling design to fulfill different requests from customers.
- Trinity continuously invests on new techniques and material. Currently the new metal powder we developed is successfully applied in different components that require high density. The density can achieve 7.4g/cm3~7.6 g/cm3( depends on the characteristics of the components).
normal density
high density
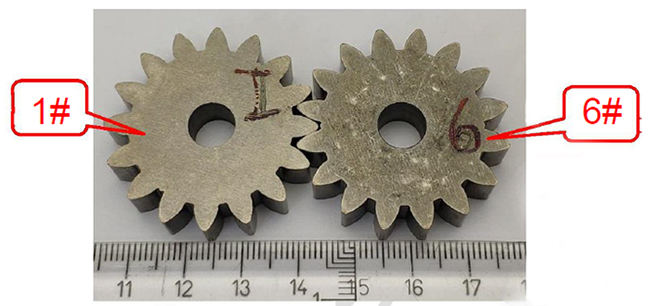
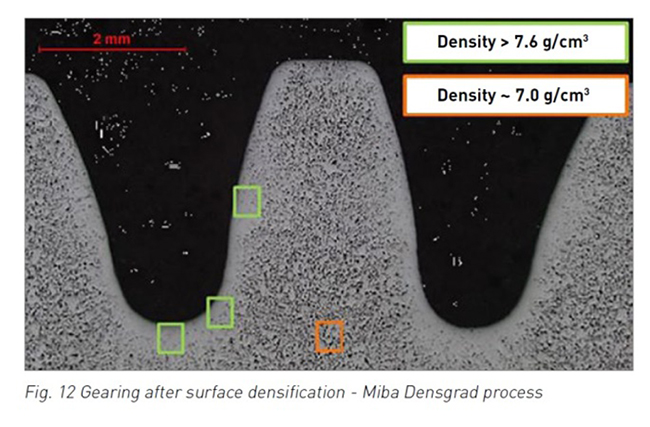
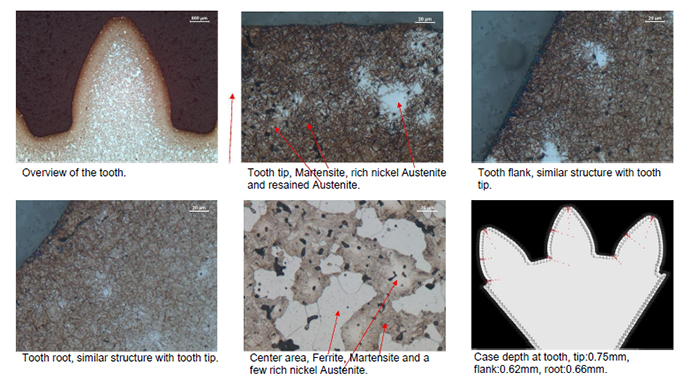
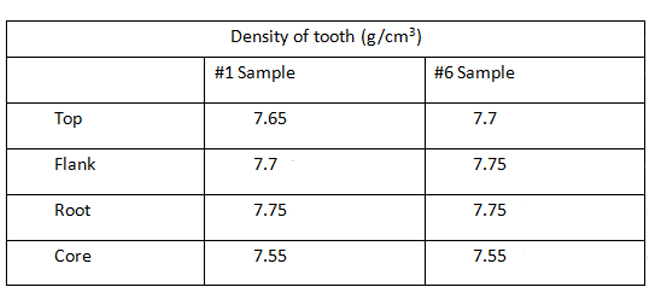
MIM (Metal Injection Molding)
- MIM solution is now a popular solution in industries like automobile, mechanics, hardware, 3C…etc.
- It has great features, like suitable for mass production, high density and higher strength.
- When some parts can’t be done by traditional PM due to difficult shape or strength requirement, MIM can be a great solution.
- We have accumulated experience over 10 years in this field.
- MIM is getting more and more popular and used widely in different fields. Trinity cooperates with experts and professors in school, and has developed the new MIM material that could reach density of 7.7~7.8 g/cm3. The high density MIM components are successfully introduced automotive industry.
Metallography of Trinity MIM ---dense and uniform
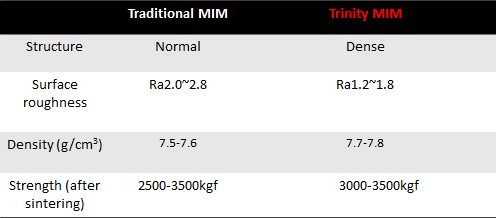
Forming Introduction
Forming is one of the basic processes in powder metallurgy production. The purpose is to use molds and presses to make loose powder into semi-finished products or finished products with predetermined geometric shapes, sizes, density and strength.
The main equipment for forming is a mold and a press. The principle of mold design is to make full use of advantage of powder metallurgy with less cutting and no cutting to ensure that the three requirements of quality (ie geometric shape, dimensional accuracy, and uniformity of density) are met. Presses are divided into mechanical presses and hydraulic presses. The mechanical press is characterized by fast speed and high productivity; its disadvantage is that the pressure is small, the stamping is not stable enough, and the pressure is difficult to hold, and it is not suitable for pressing larger and longer products. Compared with mechanical presses, hydraulic presses are characterized by large pressure, long strokes, relatively stable, adjustable speed in one cycle and pressure retention, and are suitable for pressing larger and longer products; their disadvantages are slow speed and low productivity.
Mold Of Forming
It can be divided into upper punch, middle mold, lower punch and mandrel. The number of upper and lower punches is different according to the complexity of the parts. The mold may also need two upper punches and three lower punches, referred to as upper two and lower three. Generally, the outermost punch is called the upper punch or the next punch, the second layer is called the upper second punch or the lower second punch, and so on.
Forming Steps
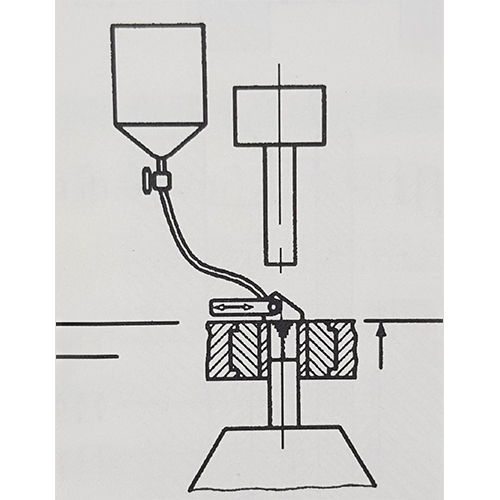
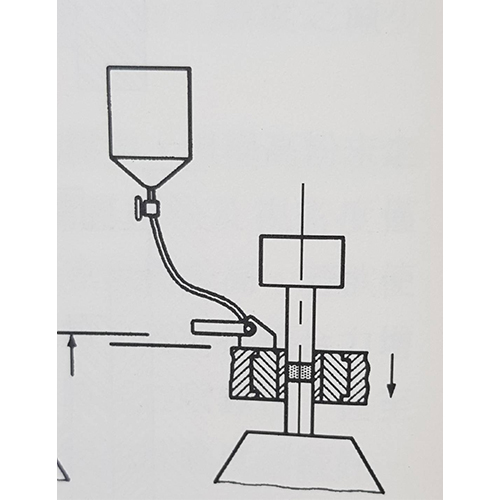
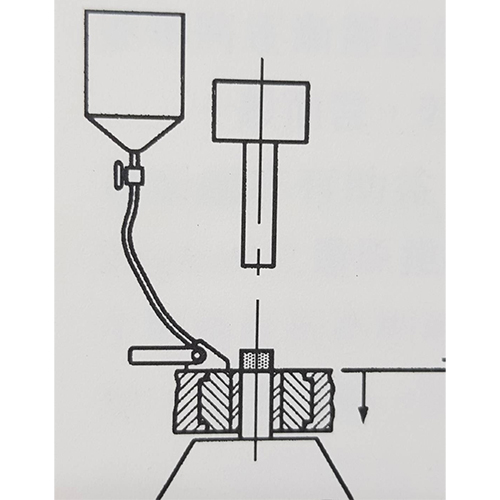
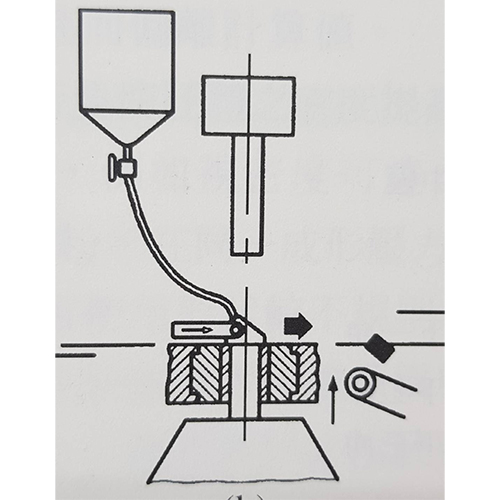
Sizing
Sizing is that the sintered parts are pressed again by the mold to make the size of the parts more accurate. The general sizing type can be divided into residual sizing type and no-margin sizing type. In terms of the outer diameter of the part, the residual sizing is that the size of the sintered product is larger than the size of the mold. By pressing the part into the mold, the excess material is squeezed into the pores and it can make the thickness of the product is thinned and the length is increased. By this method, the surface of the machined parts is smooth. Regarding no-margin sizing type, the size of the sintered product is smaller than the size of the mold, the entire length of the part is pressed during the sizing, so that the part is squeezed toward the radial space to achieve the final size.
Tumbling
At compacting process, there is always gap among molds. Therefore, burrs happen at axil direction due to metal powder existence at gaps. These burrs become stronger after sintering and might cause assembling interferences, which worsen performance. To remove burrs issue, tumbling or sandblasting processes can be applied after sintering process.
In addition, Tumbling can make the appearance color more uniform .If there is oil residual from heat treatment, color on component surface may not be even.
The principle of tumbling is to increase friction among work pieces and grinding materials (stone with different materials or liquids) thus appearances of work piece can be smoother. Varied kind of tumbling medians are applied depending on /dimension/size and shape. Main purpose of tumbling include deburring, polishing, and chamfering. And at the same time, it has a slight sealing effect on the surface of the work pieces.
Heat Treatment
Like steel, iron based PM part can process heat treatment. Heat treatment methods include carburization and nitrogen.
The distinguish difference between steel and PM part is porosity characteristic in PM’s microstructure. For PM part, during heat treatment process, very likely gas type of atmosphere will penetrate throughout the whole part. Surface hardness for PM will be similar to core hardness. Steel material normally have significant hardness difference between Surface and core because there is no pore in its structure. That is to say, toughness of PM part will be worse than steel part due to porosity microstructure. To reduce throughout hardening and to improve toughness, density increase to minimize pore proportion is a typical solution.
During carburizing heat treatment, carbon potential, quenching and tempering control are crucial process. Different production parameters lead to different strength and hardness performance. Major heat treatment process are austenitization treatment, quench and temper. The higher carbon content, the lower temperature during austenitizing period. Quench process normally use oil to quench. PM microstructure contains martensite, pearlite, bainite, depending on cooling speed and alloy contents. If cooling speed is fast during quenching process, martensite will increase. At this stage, martensite is brittle and hard. Tempering temperature is applied to improve martensite quality. After tempering, the martensitic become release stress generating from quench and improve roughness performance.