技術與專利
粉末冶金
- 粉末冶金產品多應用於汽車、家電、手工具機、縫紉機、電子、運動器材..等產業
- 粉末使用材質鐵系、銅系、銅鐵系、不锈鋼系
- 粉末產品有多孔系特性,生產含油軸承有自潤效果可長期使用免注油.
- 可製造外形複雜不易加工之產品,降低加工成本.
- 生產效率高,適合大量生產降低成本.
- 一般粉末冶金密度從5.8g/cm3-7.2 g/cm3
粉末鍛造
- 粉末鍛造為結合粉末成形與鍛造優點的技術應用。
- 它擁有增強產品密度及強度、減少材料損耗、並適合大量生產的特性。
- 目前市場上粉末鍛造的產品多應用於汽車、機械、航太…等產業中。
- 密度可達7.7~7.8g/cm3。
粉末鍛造 (PF)
metallographic Comparison
density 7.8 g/cm3
Before PF(Obvious pores)
After PF(compact structure)
鍛造
- 鍛造有增強產品衝擊強度、減少材料損耗、減少機械加工,並適合大量生產的特性。
- 熱鍛壓是在金屬再結晶溫度以上進行的鍛壓。
- 提高溫度能改善金屬的塑性,有利於提高工件的內在品質,使之不易開裂。
- 高溫度還能減小金屬的變形抗力,降低所需鍛壓機械的噸位。
高密度粉末成形
- 為因應市場對粉末零件更輕,更小,強度更高的需求,我們在高密度粉末件從原料配方的研究到成型模具的設計,都已經能自行開發生產,並提供客戶依不同產品需求的產品。
- 慶騰精密股份有限公司為市場需求不斷精進研發,已成功開發出新配方金屬粉末,可製作密度可達7.3g/cm3~7.6 g/cm3的粉末冶金製品。
normal density
high density
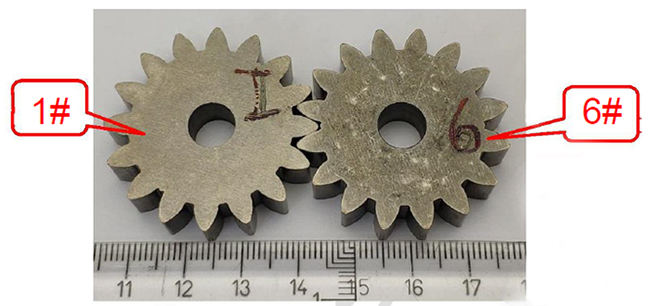
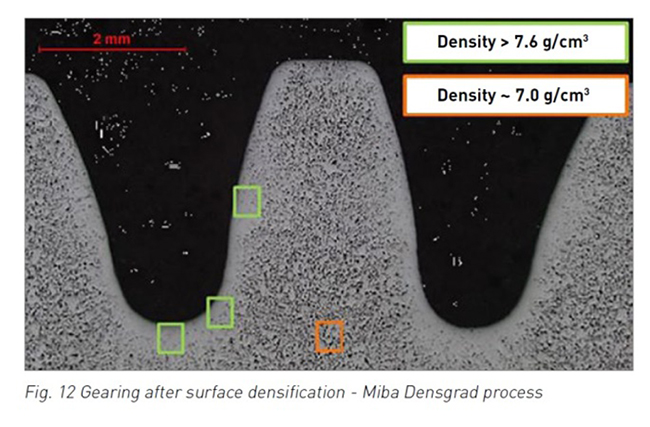
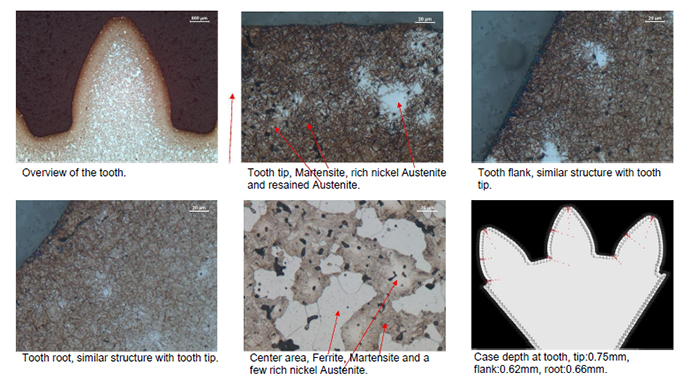
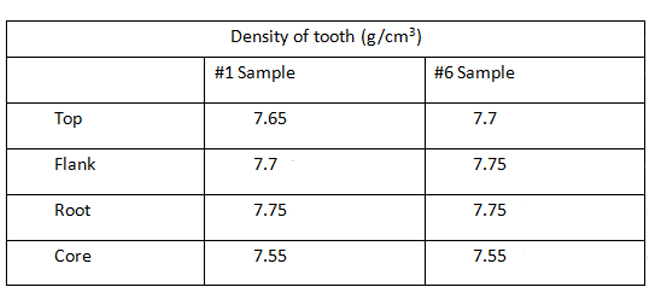
金屬粉射出
- 金屬粉末射出零件已廣泛應用於汽車、3C、機械、五金…等產業。
- 其有適合大量生產,密度高等特性,在某些一般粉末元件因形狀或強度無法滿足設計需求時,金屬粉末射出成形提供了客戶另一種選擇。
- 我們在金屬粉末射出技術已累積了十數年的技術經驗,客戶遍及汽車、3C及其他產業。
- 因應MIM應用越來越廣泛,客戶需求也愈來越多樣化,慶騰精密科技股份有限公司在原料上與產學界專家教授共同開發合作,生產出全世界密度最高可達7.7 g/cm3以上的金屬粉末配方,目前已成功推廣於汽、卡車零件。
Metallography of Trinity MIM ---dense and uniform
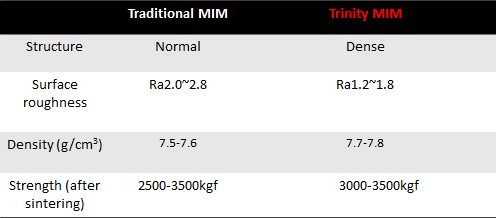
模壓成形
成形是粉末冶金生產中的基本工序之一,目的是借由模具及壓機將鬆散的粉末製成預定之幾何形狀、尺寸、密度和強度的半成品或成品。模壓成形的主要設備是模具和壓機。模具設計的原則是:充分發揮粉末冶金少切削和無切削的工藝特點,保證達到壓肧質量的三項要求(即幾何形狀、尺寸精度、密度的均勻性)。壓機分為機械壓機和液壓機兩類。機械壓機的特點是速度快,生產率高;其缺點是壓力較小,衝壓不夠平穩,保壓困難,不適於壓制較大和較長的製品。與機械壓機相比,液壓機的特點是壓力大行程長,比較平穩,能實現無級調速和保壓,適於壓制尺寸較大較長的製品;其缺點是速度慢,生產率低。
成形模具
可分為上沖、中模、下沖及芯棒,依零件之複雜性其上、下沖的數目也有所不同,最簡單之模具為一上沖一下沖,簡稱上一下二,針對複雜之模具也可能需要二支上沖三支下沖,簡稱上二下三。一般最外層之沖子稱為上一沖或下一沖,第二層稱為上二沖或下二沖,依此類推。
成形步驟
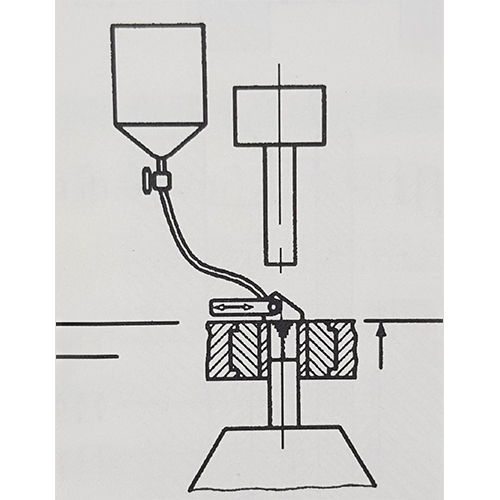
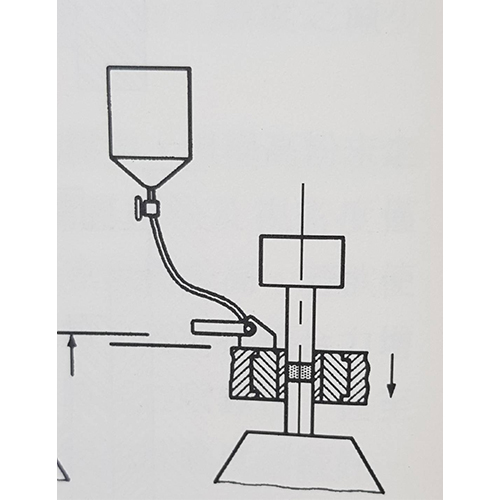
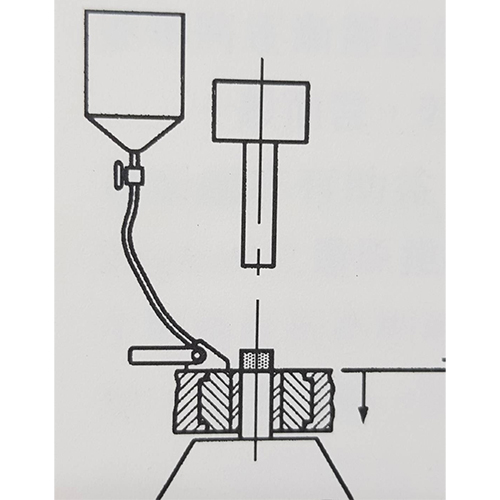
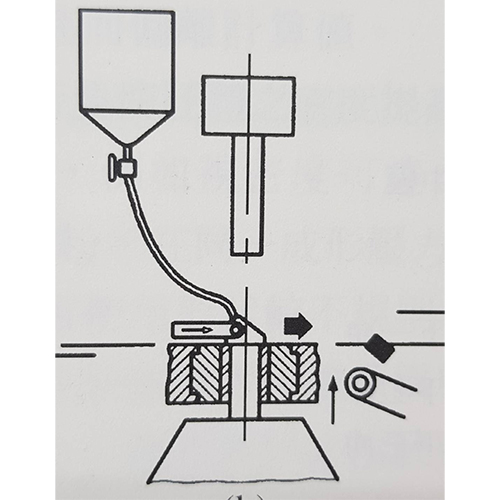
整型介紹
所謂整型就是燒結完成之零件以模具再次加壓使部分尺寸更加精準。一般整型的方式可分為餘量整型及無餘量整型。以零件外徑而言,餘量整型為燒結品之尺寸大於模具尺寸,藉由壓力將零件壓入模具內使多餘的材料擠壓進孔隙中或使肉厚變薄長度增加,以此方法加工後的零件表面光滑。而無餘量整型為燒結品之尺寸小於模具尺寸,整型時零件全長受壓,使零件朝徑向之空間擠壓來達到最終之尺寸。
振動研磨
於成形製程中,由於模具中存在著一定之間隙,使得加壓過程中細微粉末進入至間隙中,造成粉末胚體在軸向方向產生毛邊,經燒結後仍附著於胚體上,在零件組裝時易與對手件產生平涉之現象。所以一般燒結後之產品可能借由振動研磨或噴砂製程來去除毛邊。另由於產品含油可能造成熱處理後產品表面色澤不均,亦可透過振動研磨使外觀色澤更均勻。
振動研磨的原理仍連續不斷的振動,使工作槽內的工件、研磨石和研磨劑之間,因振動及翻滾而不斷的產生磨擦作用,進而達到工件所要求的表面品質。一般振動研磨所使用之研磨石會依工件的品質要求或其形狀大小,選用適當之研磨石。振動研磨的目的主要為去毛邊、抛光及倒角,同時對於零件表面具有些微的封孔作用。
熱處理
滲碳熱處理時可控制爐內碳勢及利用淬火及回火之處理來提高其硬度及強度,其主要過程為奧斯田鐵化→淬火→回火。奧斯田鐵化的溫度視碳含量而定,碳含量愈低溫度愈高。而淬火一般以油淬為主,經過淬火之工件其顯微組織大多含有麻田散鐵、波來鐵、變韌鐵相,其分佈視冷卻速率及合金成份而定,當淬火時冷卻速率較快時麻田散鐵量增加,由於淬火後的麻田散鐵硬且脆,可透過適當的溫度進行回火來改善,使其成為韌性較好的回火麻田散鐵並消除淬火時所產生的應力。